Every boring professional's purpose is to be profitable. To attain this objective, the project should be reliable and must be completed within an acceptable amount of time. These purposes call for appropriate planning, skill and also experience for those accountable and also of those on the task that operate the equipment and also a selection of other devices.
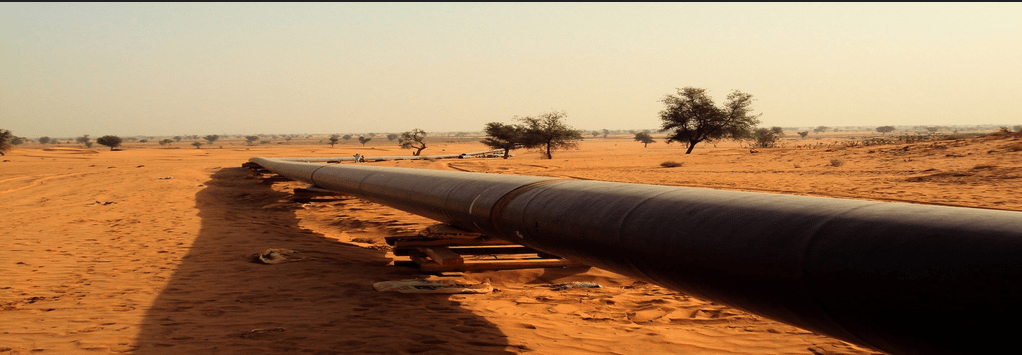
From a professional's perspective, there can be little benefit in any failings of equipment or tooling. Revealed market tooling failings do lead, however, to the discovery of different treatments for attaining future drilling success.
Tooling failures are frequently the outcome of unusual or complex problems which arise from unidentified risks-- hazards that do not take place in directional boring. Other failings are frequently the result of techniques in the production procedure. Experience, for which there is no replacement, is type in directional drilling. Just like other specialist endeavors, professional drill use depends upon expertise and skill, which is established gradually.
Mud motors in high PSI applications are important in straight drilling. The complying with are 5 pointers in manufacturing procedures for preserving performance in using mud motors in the directional horizontal directional drilling services procedure of resource extraction.
First, stay clear of delaying the motor, as a motor delay generally indicates that the fluid circulation has actually quit electric motor rotation. This can be the result of raised drive while in contact with the rock or cutting face, protecting against motor rotation. This kind of motor delaying forces fluid via the blades and stator assembly without any rotation, which subsequently brings about damages of both the electric motor and the pump.
Second, lessen abrasives in the fluid as long as possible by keeping all screens clean and also in good condition. Performance is a feature of resistance between electric motors and various other tools like the stator. All abrasives in this process are moving at high pressure with the motor, causing wear, minimizing torque and, eventually, total efficiency.
Third, be prudent by executing maintenance on an once a week basis or at around 100 hrs of use, for the straightforward factor that relocating parts in motors wear. Often it might appear that spending plan or production schedules demand foregoing scheduled upkeep. Keep in mind, though, that straight directional exploration devices normally damages at the incorrect time and fixings can be really pricey. A lot of failures can be prevented with systematic upkeep; it seldom pays, in the long run, to miss it. Efficiency depends upon team effort and also on the collective procedure of men and also the equipment they utilize. In drilling, and especially in straight and directional boring, this consists of a myriad of parts: bearings, rotor, stator, and so on. Normally, if maintenance is not done once a week or after just a hundred hrs or two, the equipment's full efficiency will reduce and prices of service will increase. If the equipment breakdowns or breaks as a result of not enough upkeep, the cost will certainly be also higher.
Fourth, keep in mind that tasks may show up successful when exercised on paper, yet that success on an active freeway or other possibly unsafe job website is an additional issue. When a dangerous job is currently over budget plan and also past its completion time, with others waiting impatiently for the job to be finished, earnings can go down or evaporate entirely. There are circumstances in which tooling has actually justifiably been sacrificed to complete the birthed, simply to get the task done. These are not circumstances, however, that anybody locates sufficient or successful in the long run.
There are lots of instances in which reliable practices in fact increase the crew's efficiency as well as reduced expenditures in conclusion, while reducing tooling prices of the overall holes drilled. These are the procedures that incorporate the previous suggestions for tried and tested success in running directional drilling over the long haul.